B/S/H Home Appliances Group
132,000 LITERS OF WASTE That's how much the autonomous MiR robots transport within 24 hours at the B/S/H warehouse in Rzeszów. Thanks to comprehensive integration of hardware and software in the company, the waste collection and disposal process has become more efficient and automated.
Location: Rzeszów
B/S/H is a company offering high-quality home appliances and digital services. In 2021, B/S/H approached us to optimize the waste disposal process in their warehouse in Rzeszów. Thanks to comprehensive integration of the following hardware and software, the company implemented pioneering solutions supporting process automation and technological transformation.
Comprehensive solution implemented in the B/S/H warehouse in Rzeszów enabled exceptional automation, that ensured unmanned emptying of 120 1100-liter containers within 24 hours. 3 autonomous robots retrieve waste containers from designated locations, then transport them to the waste collection area and empty the contents directly into the compactor. After emptying, the robots efficiently return the containers to the collection point, ensuring process continuity. The system handles a total of 24 containers and 4 bins placed in special docking stations, located in 20 locations in the warehouse. Each station is equipped with an order monitoring cassette and electromagnets to secure the containers during loading and ensure operational safety. A key element of this solution is the SUPERVISOR software, which actively monitors the stations and locations where robots deposit containers. This allows B/S/H to optimally utilize the robot fleet, control container availability, and manage the waste disposal process. This software also allows for task reservation and queuing, as well as utilizing other advanced functionalities, enabling flexible adaptation to the company's changing needs. Robots at B/S/H are equipped with the DORSAL docking module, allowing the robot to drive under the platform with any enclosure, latch onto it, and deliver the trolley to any location. During operation, robots encounter significant traffic, including forklifts, operators, and so-called milk runs. Thanks to scanners and a 3D camera, robots agilely navigate obstacles and continue their route collision-free.
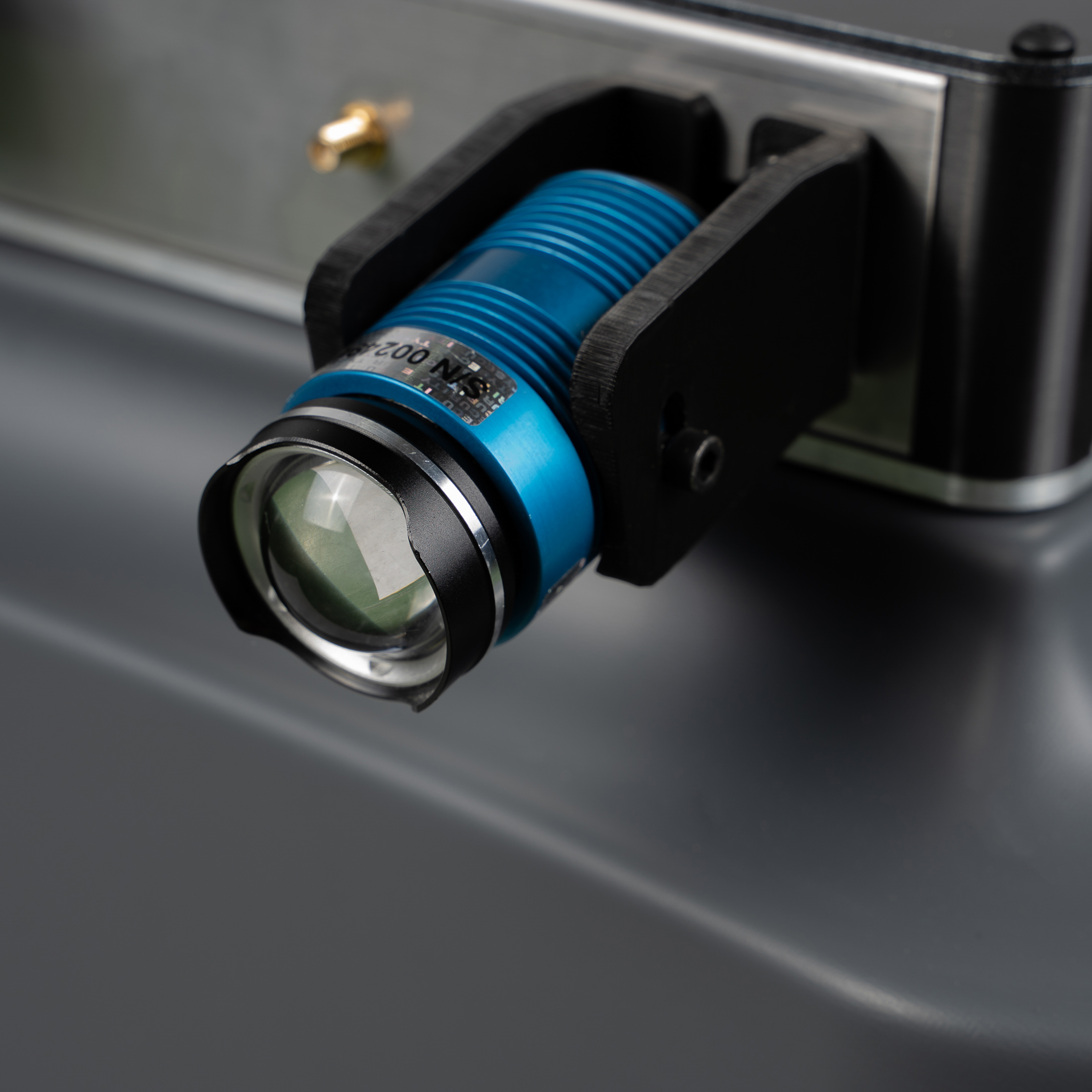
Spot lights kit
Visual LED warning system for mobile robots
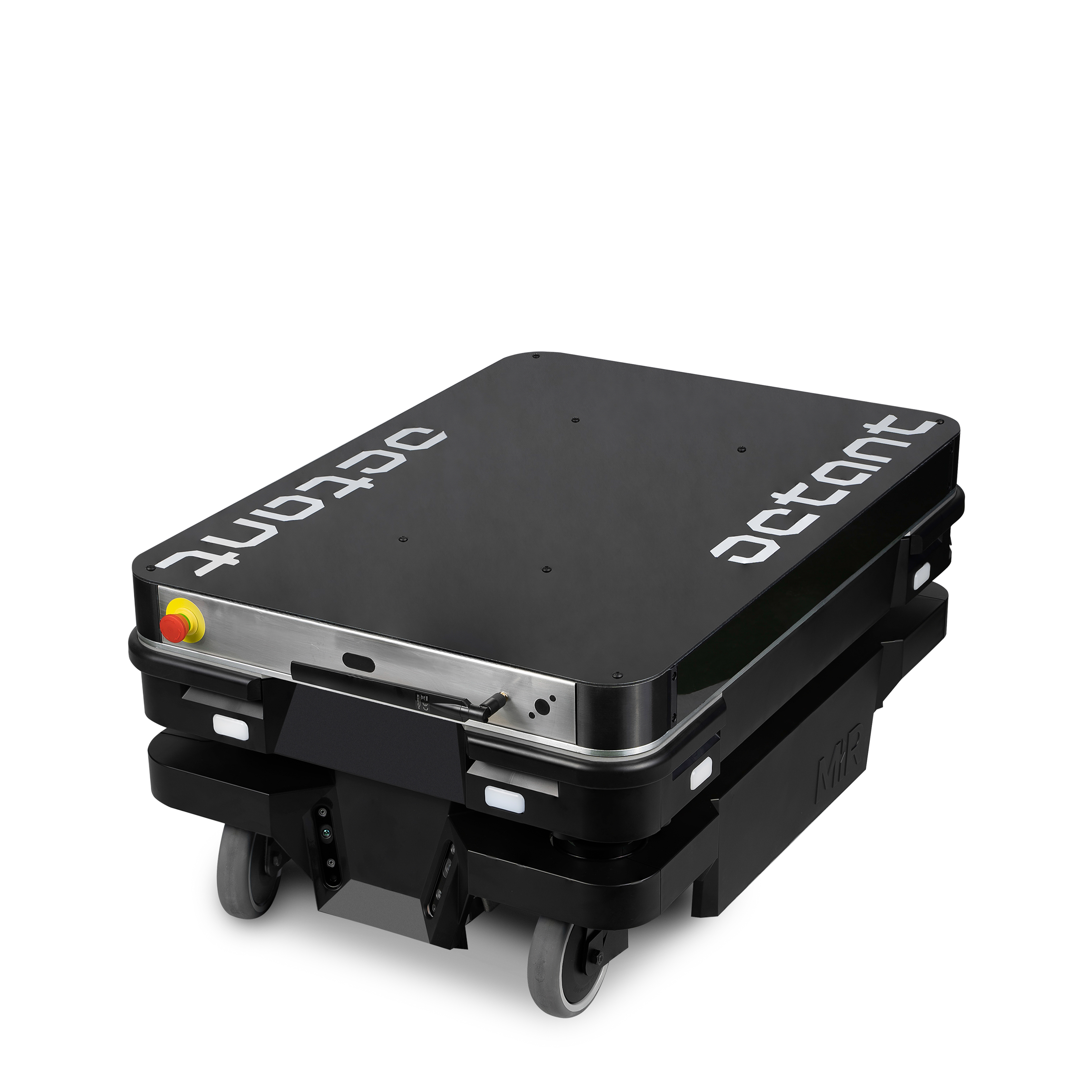
Dorsal 250
Platform transport module
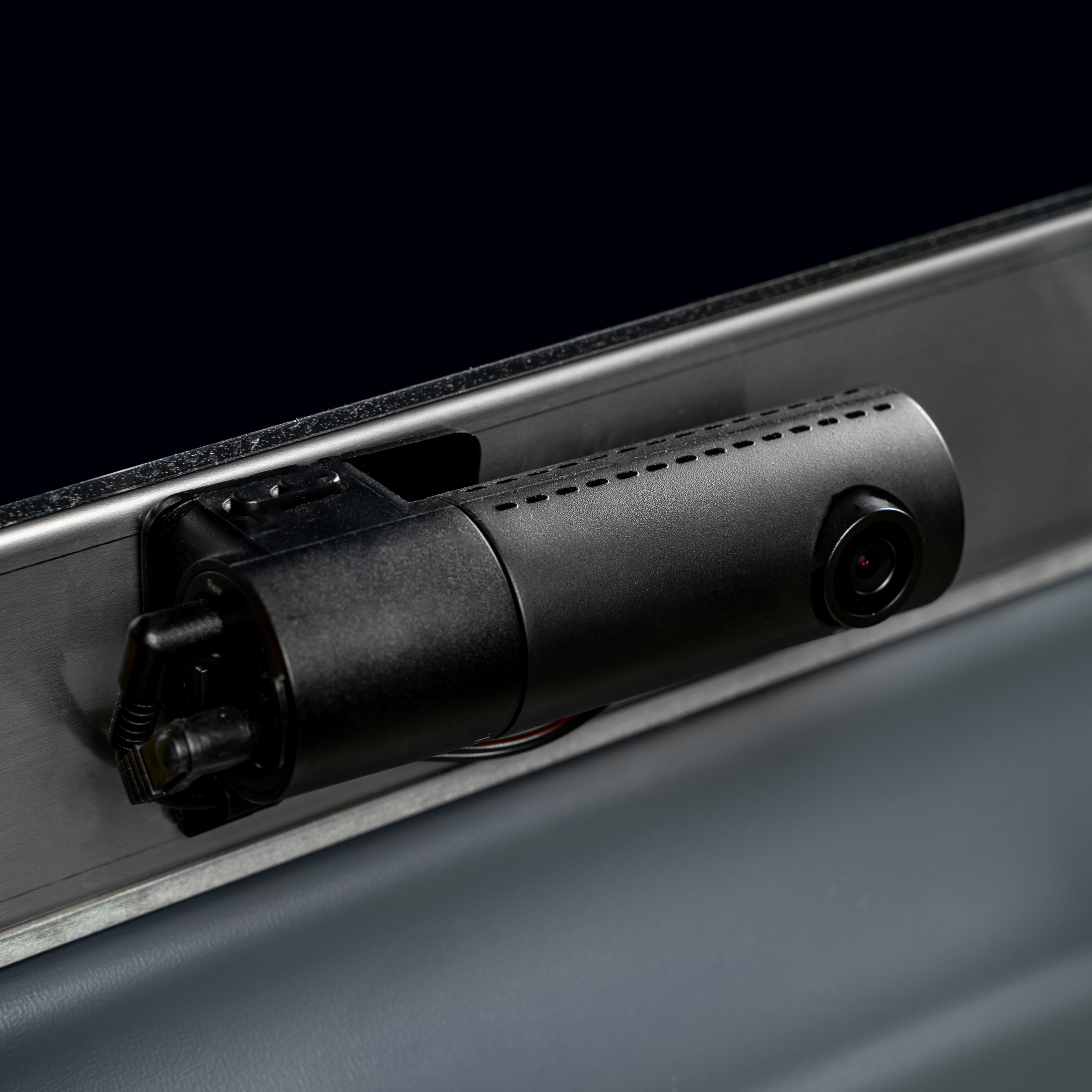
Dashboard camera kit
Cameras recording robot operation for up to 48 hours
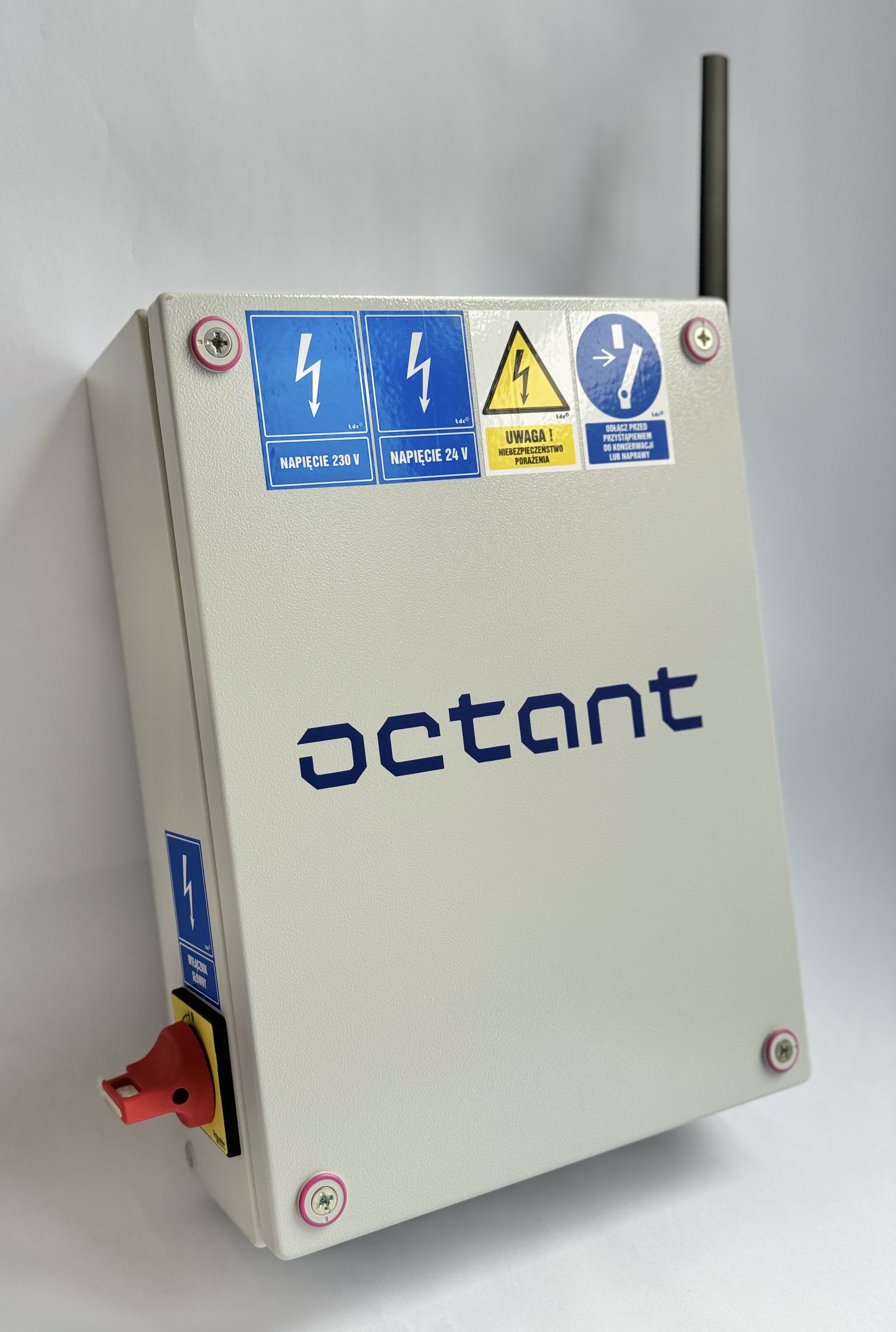
SmartBox
It allows for connecting any device to the robot system
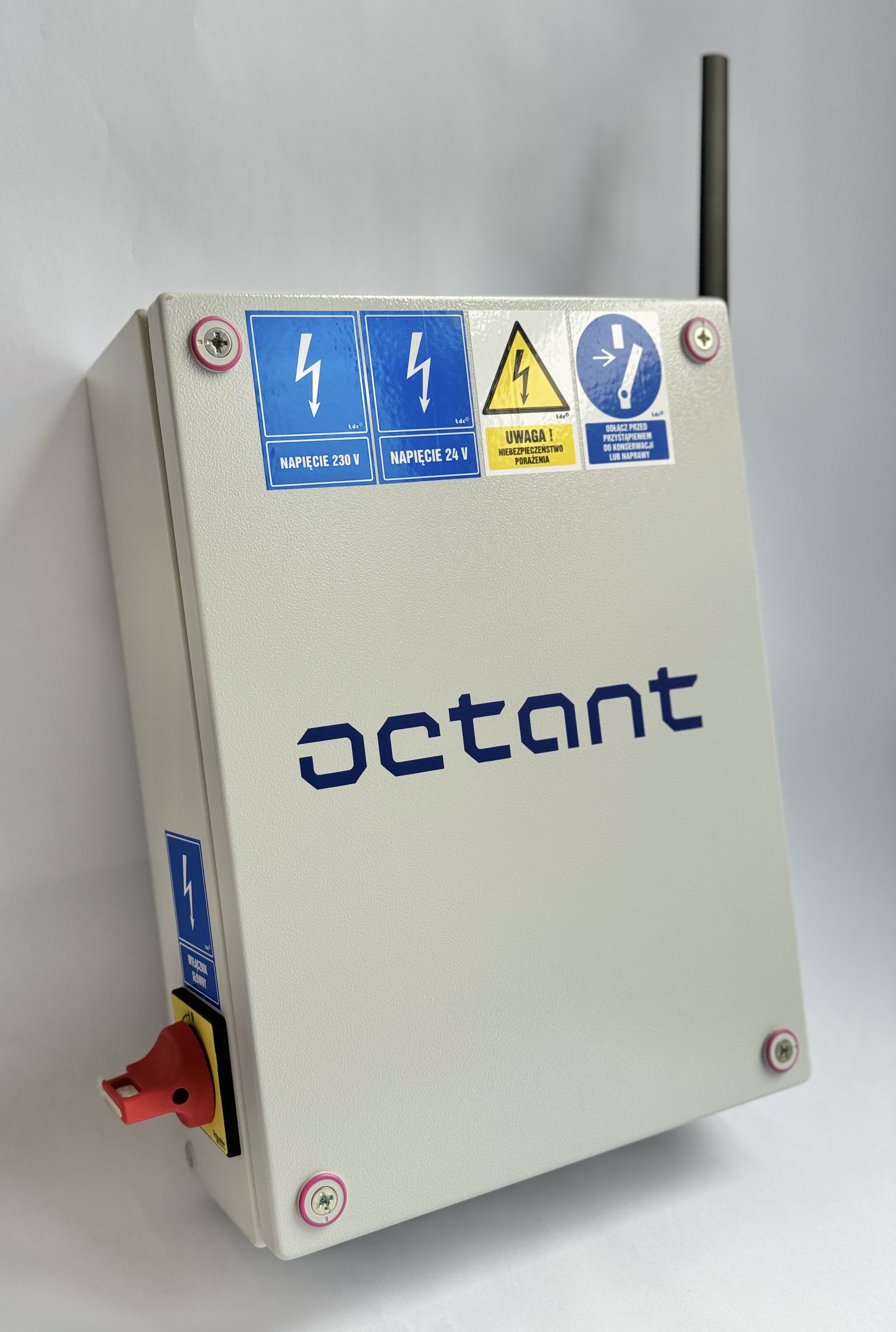
SmartGate
Supports communication between robots and industrial gates to enable automated transport operation.
Statistician
Analysis of data from mobile robots and IoT devices
Supervisor
Comprehensive handling of transportation processes
3 Robots
MiR 250 equipped with the top module Dorsal
120 emptied containers 1100l
within 24 hours is the maximum throughput of the system
150 meters
is the average loop of each robot
CASE STUDY
Leoni Wierzbice
Autonomous forklift
Over the course of the year, it transported over 10,000 tons of products and completed 15,000 100-meter runs, reaching areas where conventional forklifts cannot fit.
CASE STUDY
Whirlpool Corporation
Automated transport of semi-finished products from the preparation area to the production line.
3 MiR robots with Dorsal docking modules ensure smooth delivery of components, aiming to increase the efficiency of the production line by delivering parts at the right frequency.
Products:Dorsal 100/200Dashboard camera kit